You have no items in your shopping cart
Types of Distillation
- Posted on
- By Goldleaf Scientific
- Posted in How To Guides, Short Path Distillation
- 1
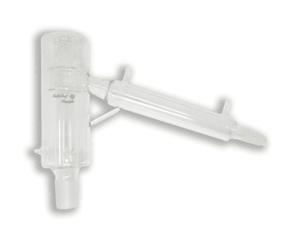
There are many different ways to perform distillation each with its own positives and negatives. It can generally be stated that purity comes at the cost of speed and so fast systems like a wiped film distillation usually aren’t for fine separation of components and slower systems like fractional distillation are generally for greater separation.
Simple distillation- Just a boiling flask head, condenser, and receiving flask (sometimes referred to as a pot still). The sample is heated in the boiling flask and turned into vapor. Then it goes to the condenser and is turned back into a liquid and flows to the receiver flask. The speed of distillation can be high, but the degree of separation is quite low and this type of distillation is generally only used when the boiling points of the components in a sample differ by 40° C or more.
Short path distillation- The length of distance that the vapor molecule travels before being condensed is short and thus referred as a short path distillation. The greater the distance the more heat needed and so short path distillation apparatuses are used to limit the heat needed for distillation. This is often due to a sample that will degrade at elevated temperatures and so a reduction of path length and pressure is often used to reduce operating temperatures and degradation. Wiped film machines with an external condenser would be considered short path, a kugelrohr, or even a standard pot still would as well. Many systems can be called a short path device and as long as the path length is reasonably short the name is fitting. A kugelrohr is essentially two flasks joined together in which the sample is heated in one then cooled and condensed on the other. The flasks are rotated fully or back and forth to spread the sample onto the walls of the heated flask. The large heated surface area and short path makes the device ideal for distilling components below their boiling points.
Molecular distillation- In this instance the path length is extremely short. This obviously reduces the temperature needed for a distillation, but the path is so short and direct that regardless of the direction the molecule is forced to hit the condenser. This is important because at high vacuum levels (<20 micron) molecules, once vaporized, can travel in any direction even the opposite of the flow of vacuum. This is called molecular flow and is very different from the way molecules travel at lower vacuum levels. In the case of lower vacuum level, the molecules hit other molecules and transfer momentum and so on until the distribution of molecules and thus pressure is equalized. Oil molecules flowing in the opposite direction from the vacuum pump into the distillation apparatus is called back-streaming and can be eliminated with vacuum traps.
Fractional distillation- Incorporates a fractional column between the boiling flask and the condenser. As vapors rise up through the column they condense on some packing material or vigreux teeth in the column. The new fresh rising vapor re-distills that material which again condenses and distills multiple times, each time increasing the separation of components. The components with higher boiling points eventually make their way back to the boiling flask and the components with lower boiling point are carried over to the condenser.
Thin film distillation- Material is fed to the top of a heated cylinder where a blade or roller spreads the sample into a thin film along the wall of the cylinder. The sample is then vaporized from the wall to a condenser. The short residence time of heating and extra thin layer makes it ideal for limiting degradation while distilling viscous products.
Pros:
-
Fast distillation
-
Reduced degradation
Cons:
-
High equipment cost
-
Limited separation capabilities
-
Increased time spent of material preparation like degassing
Short path distillation- Bench top short path systems like the ones we sell here are a great middle ground between distillation speed and fractional separation. They can be scaled up to 20L and are capable of speeds that can match a smaller wiped film system. They have a fractional column for increased separation abilities and significantly smaller upfront cost.
Pros:
-
Fast distillation
-
Good separation
-
Low upfront cost
Cons:
-
Possible risk of degradation
Spinning band distillation- Uses a long fractional column with a spinning band that forces the rising vapor and falling liquid to come in closer contact which increases efficiency and separational capabilities in the fractional column.
Pros:
-
Finer separation of compounds
-
Higher yields
-
Consistent high purity
Cons:
-
High upfront cost
-
Slow distillation rate
-
Complex setup and operation
PhD in spinning band acethonitrile