You have no items in your shopping cart
What is a Glass Reactor and how does it work? In-Depth Guide To Glass Reactors
- Posted on
- Posted in Buyers Guides, Glass Reactors, How To Guides
- 0
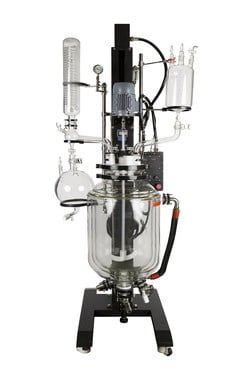
What is a glass reactor?
Scientific and research labs require controlled environments to conduct certain studies and processes. In order to facilitate this entirely controlled environment, researchers will employ glass reactors. These are vessels that range from small (500 milliliters) to large (150 liters+) sizes depending on the volume of the experiments. By connecting a glass reactor to external equipment such as heaters, chillers, vacuum pumps, and stirrers, researchers are able to control every aspect of their experiment. We will go over the exact components, variations, and uses of glass reactors throughout this article. (Read more below)
Featured in this article:
Goldleafs Line of Chemical Reactors
How does a glass reactor work?
A laboratory glass reactor is used to facilitate chemical reactions with air and temperature control. They implement a lid that caters to a number of accessories like stirrers, condensers, and thermometers. Solutions and reactants are loaded into the glass reactor body and the reaction process is monitored through the clear glass for visual cues. As the reaction progresses, it is adjusted by altering certain variables like temperature, stirring speed, and pressure.
-Components on a Glass Reactor
There are numerous different pieces of equipment that can be paired with a glass reactor set up. We will likely create an in depth article about selecting things like the proper heating and cooling systems in the future. This is mainly because the ancillary equipment needed is determined entirely by the application of the end user, which you will see later in this article can be a number of different uses.
Let's start by breaking down the different types of equipment that can be used with reactors. For starters, there is the equipment that is included with a Goldleaf Reactor purchase, such as stirrers, feed flasks, and condensers.
As stated in the above section about available Goldleaf models, there are several types of stirring motors. A stirrer with standard components is used for aqueous solutions like testing soil solubility in water. Explosion proof stirrers are commonly paired with a fume hood for use with volatile solvents like ethanol. These are electric stirrers with sealed components that can withstand flammable fumes and not give off a spark. For extremely volatile compounds like pentane and other hydrocarbons, air powered stirrers are connected to a compressor so there is no electricity near the reactor at all. Reactors with air powered stirrers are often placed in C1D1 explosion proof booths with fire suppression systems, exhaust vents, and gas detectors.
Feed flasks are used just as the name implies, to feed solution into the reactor. This glassware can have multiple uses such as drip feeding more solvent into a mixture and measuring feed stock before loading.
The condenser that comes with a Goldleaf reactor is meant to be used as a reflux condenser. Placed vertically above the reactor, any fumes created in a reaction mixture will travel upwards through the chilled glassware, re-condense, collect, and drip back into the reactor. Depending on the gas being released, a certain type of chiller cooling system will be required.
Glass Reactor Models
Here are a few models of Goldleaf glass reactors to give an idea of what options are available. All of our reactors come with an overhead stirrer, controller, and condensers with size options from 10 liters to 150 liters. Lids are sealed with chemically resistant ptfe gaskets.
Benchtop Reactors
(500ml, 1 Liter, 2 Liter, 5 Liter sizes)
Benchtop reactors are smaller sized units that can fit on a table or under a fume hood. Their smaller size allows for testing of processes before scaling up, or production of small amounts. Usually benchtop reactors range from 500ml to 5 Liters, then jump to 10 Liters for pilot scale.
These models do not have any explosion proof options as they can easily be placed under a fume hood for ventilation, which is usually less expensive then upgrading to C1D1 grade components. All benchtop reactors come with options for single or double jackets for temperature control and insulation.
Goldleaf Single Jacket and Double Jacket Glass Reactor
(10 Liter, 20 Liter, 50 Liter, 100 Liter, 150 Liter sizes)
Our standard, base model reactor, the single jacket has an outer layer allows for a connection to a recirculating chiller or heater. A well priced, versatile unit that can fit a number of needs from L2L extraction, distillation, and bulk heating and cooling.
A step up from our single jacketed glass reactor, the double jacketed model comes with everything the base model has but with an extra layer. This second, outermost jacket can have vacuum pulled on it to completely insulate the inner layers and prevent energy loss to the surrounding environment.
Optional Air Powered Motor
For those using volatile substances, our reactor have an optional C1D1 rated air motor that is powered by an external air compressor rather than electricity. An important thing to keep in mind when buying and setting up this reactor, is having a proper sized air compressor that is far enough away from the vessel for safe use. Size of the air compressor depends on the size of the reactor.
Goldleaf Jacketed Explosion Proof Glass Reactor
When dealing with any flammable substance, an explosion proof motor is almost always required. The electronics on this model are UL rated and marked for use in C1D2 environments. This reactor uses a brushless geared DC motor. When paired with a fume hood and other safety precautions, this reactor is well suited for use with volatile and flammable substances. Always check with the regulatory licensing agency in your area to ensure you meet local fire codes. Goldleaf can always help with making sure your reactor is up to code.
Goldleaf Lifting Reactor
(10 Liter, 20 Liter, 50 Liter, 100 Liter, 150 Liter sizes available)
Goldleaf Lifting Reactors create a new level of efficiency and ease unseen in other models across the market. An electric lifting motor in the stainless steel frame gently lifts the glass lid. This lift means none of the ancillary glassware needs to be removed when opening the vessel. Any condensers or manifolds will easily rise with the lid making this process much easier.
Once the lid has been raised to its height, a hand crank allows users to tilt the main reactor vessel. If there are any solids in this reaction their removal is much easier when the body is tilted. The same goes for cleaning and any other maintenance that may be required. Reactor bodies can be rotated a full 180 degrees with no strain on the user.
Filter Reactors
(500ml - 5 Liter, 10 Liter, 20 Liter, 50 Liter, 100 Liter Sizes Available)
Building Your Lab Reactor - Customize Your Reactor System
Laboratory reactors are intricate pieces of equipment that apply to various different applications, most of them are so specific that there could never be a “one size fits all” solution for lab reactors. Every process and every lab layout is different, meaning each reactor system must be adjusted properly. At Goldleaf Scientific, we have unique customization options most other suppliers do not offer. Not only can we help design your system, but we can make custom changes and upgrades with our manufacturing capabilities. Our shop is fitted with a glassblowing studio, machining for ptfe and metal, along with assembly capabilities such as making a custom explosion proof reactor fit your local standards and fire code.
Standalone reactors will always be one of our specialties, but we can also help users design custom skids. If a process requires feeding from a large tank, we can customize the connection options to make sure the reactor hooks up properly. Same for the drain port if the reactor is emptied into another system such as a solvent evaporator for recovery. Our setups can fill a reactor, mix or homogenize the solution as needed, and empty into our rotary evaporators or other post processing equipment.
Planning your reactor
There are a few basic questions to account for when planning your reactor skid design. Consider your mixing needs, will an overhead stirrer do, or do you need to emulsify oils and waters with a homogenizer? If working with solids, how thick will the solution be, and do you plan to break down these solids into smaller particles?
Heating and cooling are key elements of a reactor, so consider the need for temperature control. Do you need a heater or chiller to control the temperature?
What kind of solvent are you using? Is it so corrosive you need special gaskets and seals? Or is the solvent so volatile you need a fume hood? When this solvent evaporates, do you plan to recondense it back into your solution, or separate and remove the vapors entirely? Does this solvent or process require a vacuum pump, and what type of pump is needed?
Asking yourself these questions before moving forward is key to understanding your needs in equipment. Do not worry, we will get more in depth with each of these questions as we start planning the reactor build out below.
Step 1 - Choose Size
The size of the reactor will obviously relate to the scale of your process. Are you mixing a couple liters at a time for testing purposes, or doing a large scale reaction for production purposes, say 50 liters or more? When deciding the size of your reactor, account for extra headspace that will be used when stirring or evaporation of solvents.
We carry sizes from 500mL to 150L+, for reference, anything over 10L is referred to as pilot scale size, and any reactor smaller is considered a benchtop model.
- 500ml
- 1 Liter
- 2 Liter
- 5 Liter
Key characteristics of a benchtop laboratory reactor include:
1. Smaller Size
These reactors can be placed easily on tables or under fume hoods for volatile solvents. Typically, they have capacities range from 500mLs to 150 liters.
2. Controlled Environment
Benchtop reactors provide a regulated environment where temperature, pressure, agitation, and reaction duration are carefully controlled. This level of precision enables researchers to adjust reaction conditions.
3. Multiple Uses
Benchtop laboratory reactors are versatile, applying to a wide range of chemical reactions including chemical synthesis, crystallizing, filtering, testing, and more. Various designs offer different stirring methods, thermal regulation systems, and monitoring instruments tailored to specific reaction requirements.
4. Safety Features
Benchtop reactors come with safety measures designed to prevent accidents and protect personnel. Including temperature and pressure sensors, mechanisms to relieve extra pressure, and emergency shutdown protocols.
Benchtop laboratory reactors are essential tools, allowing for controlled experimentation, optimizing processes, and research. Contributing to advancements in diverse fields from pharmaceuticals to cosmetics and material science.
Step 2 - Choose Your Frame
The stainless steel frame is the foundation of any reactor skid. Based on what type of reactor you need, you will determine the exact frame required. Usually these come together with your choice of body style and size, but it is important to understand the varieties of frames to decide exactly what reactor build you will move forward with.
Standard frame is a stainless steel scaffold that firmly hold your reactor in place. Usually fitted with caster for easy transport, these frames are most common and used with systems that use easy to clean liquids.
Lifting frame is fitted with the ability to lift your reactor lid and lower or tilt the reactor body for easy collection of solids or crystals. When using a large or crystallizing reactor, having the lift is absolutely needed for reaching into the bottom of the reactor to scoop out solids or clean off the surface. Usually, anything larger than a 10L reactor body is fitted with a lifting frame unless otherwise stated. Some reactors use hand powered cranks but these take time, while an electric lifting reactor raises or lowers at just the push of a button.
Filter reactor frames are slightly different. If you plan to filter your solution immediately after its time in the reactor, we recommend using a reactor with a built-in filter plate at the bottom. By doing so, users eliminate the need for an additional filter setup. Filter reactor frames come in standard or lifting options depending on what the process looks like.
Step 3 - Choose the body style
Jacketed reactors use an extra layer of glass insulation to maintain a constant set temperature decided by the user. A recirculating heater/chiller will pump fluid through this external layer of glass and ultimately raise or lower the temperature of the solution on the reactor. Any reaction or process that is temperature sensitive will require a jacketed reactor and a heater or chiller, which we will discuss in a later step.
Single Jacket reactors have one extra layer of glass around the reactor body. These are usually more cost effective options for users that do not require precise temperature control, but rather just need to keep temps within a certain range. These bodies are good for keeping things warm or cold, but may struggle to keep exact temps due to the energy loss from the ambient room temperatures.
Double Jacket reactors have an extra layer of vacuum insulation surrounding the inner layer where the heat transfer fluid flows. This extra vacuum layer is useful for multiple reasons, firstly it lowers energy costs by retaining heat or cold within the reactor, rather than losing it the the air in the lab. Also, when a reactor is used for extremely cold processes, this second layer prevents any condensation from fogging up the glass and obscuring the view of the solution. For users who need exact temperatures dialed in, a double jacket reactor is their best option.
Step 4 - Choose Stirring Motor
Every reactor setup comes with a stirring motor of the user's choice mounted atop the reactor vessel.
A standard model is a high torque, electric stirrer with digital controls. To upgrade from here, the next step is an air powered motor. An air powered motor is a budget friendly option for processes that use volatile solvents that give off potentially flammable vapors.
An air powered motor will be connected to an external air compressor, thus there will be no electronic motor giving off a spark right above the reactor. Keep in mind that these motors do require a high powered air compressor to operate, which can be useful to operators that already have a compressor for other uses.
Finally, an explosion proof motor is also used when flammable vapors are present, but is ideally wired directly into the wall of the facility. An explosion proof motor is electric but sealed so no vapors can ignite. When using any forms of volatile vapors, we highly recommend adding a fume hood to deal with vapors from filling and draining solvents. Even when using a standard motor, a fume hood could be enough to deal with vapors and thus not require an additional upgraded motor.
Step 5 - Choosing an impeller
There are a a wide variety of stirring shafts for reactors, from food grade for beverages to industrial for strong chemicals. Take into account the material of the impeller shaft, is ptfe best for a food grade mixture, and stainless steel better for corrosive chemicals? Start by deciding which material is best, then which type of blades or paddles should be on the end.
Paddle shafts are best for mixing solutions, when basic stirring is enough. When dealing with solids, a sharp bladed end can break up materials and blend them into a solution. Listing all of the types of impellers here would overwhelm this article, so be sure to research or call in and ask what type of shaft paddle works for you.
Step 6 - Choose Your Heater or Chiller
For users who only need to warm up a viscous solution to make it easier to stir, a recirculating water heater should suffice. As for those who must chill their solution for degradation, a recirculating oil chiller can keep a reactor cold. However, as temperature requirements become more precise, the heater or chiller must be able to accommodate this. If a user needs to maintain tight temperature ranges, a high powered heater chiller combo is best as it can warm or cool the vessel as needed. Whereas a sole heater or chiller must wait for the energy to escape into the room for changing temperatures, which may take too long and lead to wild swings in heat. Choosing the proper heater or chiller is actually quite in depth when taking into account things like power requirements, chilling power, Kw’s of heating, and more. At the end of this blog is a link to an article detailing how to decide the best heater or chiller for your system.
-Chiller Cooling Systems
A recirculating chiller will serve a number of purposes for a glass reactor. Not only for chilling any condenser, but mainly cooling the jacketed layer of a reactor. A smaller, 10-20 liter reactor that will only require cooling, can utilize a benchtop chiller, for example a Polyscience 40C to -20C LS Benchtop Circulating Chiller. With the ability to reach -20c with slight heating power up to 40c (104f), this unit will be able to cool smaller reactors with no heat load and even raise temps above the ambient room temperature if needed.
Larger reactors are regularly used for multiple purposes, especially in testing and research labs. Meaning these setups will require both heating and chilling to accommodate certain applications. For applications that require mainly chilling, there are units equipped for high strength cooling with some heating. This Lauda Ultracool UC14 Chiller has a very strong cooling capacity at -20C and will easily cool a larger, 100 liter reactor system.
-Recirculating Heaters
Depending on the application, a strong heater may be needed for distillation, decarboxylating, and dissolving certain solutions. Users who are trying to mix small batches of viscous solution may need slight heat to make a substance easier to work with. Volumes around 10-20 liters will suffice with a Polyscience 7L Open Bath Recirculating Heater, which can reach up to 200C with 1kw of heating power. This unit would be great for keeping things warm and even boiling small amounts of solvent.
Polyscience 7L Open Bath Recirculating Heater
As things begin to scale up to 50 liter and large reactors that demand high temperatures for distilling gases and de-carbing oils, a much more powerful heater is needed. Not necessarily a larger heater, but certainly one with more kw heating power. A Huber CC-315, open bath heated circulator has 3.5kw of heating power with a 300C range. Reactor kits that demand constant high temperatures will benefit from a heater like this or stronger.
Step 7 - Choose Your Vacuum Pump
If this system must be vacuumed down for any reason, whether to remove oxygen that would cause degradation, or to control the flow of vapors, a vacuum pump must be chosen. If there are corrosive solvents being used, a specialty pump will be needed to handle these corrosive vapors without breaking or causing a fire. Ultimately, the strength of the vacuum pump will be decided on the size of the reactor, and the depth of vacuum that must be achieved. At the end of this blog is a link to an article detailing the various types of vacuum pumps and how to select yours.
Step 8 - Choose a Vacuum Manifold and Controller
Once you have selected a vacuum pump, it is important to decide how to connect it to the reactor. Is the vacuum pump being connected to any other systems? If so, a manifold with multiple valves and connections will be needed to link one pump to various systems. Consider how you will throttle the strength of the vacuum pump, you will need to be able to control how fast the pump is pulling air out of the system. At the very least, a user should use a handle needle valve to choke the flow of the pump and open it as needed. Ideally, there would be an electric vacuum controller that has programmable settings that maintain exact vacuum levels without a technician. As for any vacuum pump, a vacuum gauge is absolutely necessary, such as a digital vacuum gauge.
Step 9 - Choose Your Condenser and any Additional Glassware
The condenser you select is based entirely upon what you plan to capture. For instance, if there is no vacuum pump connected to the system, and no need to separate vapors from the solution, then a reflux condenser is perfect. A reflux condenser will capture any vapors that make their way out of the solution, recondense them into liquid, and return them into the reactor vessel. However, when there is a vacuum pump connected, these volatile vapors cannot be allowed to make their way to the pump. Wherever the pump is connected to the reactor, a condenser or cold trap must be used to condense the vapors back to liquid state before they pass onto the pump as volatile gas. Also, if the vapors of a solvent are meant to be removed and stored separate from the solution, a sideways or tilted condenser will be angled in such a way to capture these vapors and condense them into a different collection vessel, thus acting as solvent recovery. Determining glassware needs can be difficult and we are available to assist in the production, selection, and design of any additional glassware for your setup as these are the final steps of the reactor skid.
Plumb Your Reactor
Are you feeding your solution from a large feeding tank? Is the solution being drained into a separate system such as a rotary evaporator? Are you planning any post processing filtration? These questions will decide how the reactor will be plumbed to any external systems. A reactor can be used as a stand alone unit, but is more commonly one piece in a larger system used for refining, extracting, crystallizing, or filtering bulk solutions.
Designing and planning a reactor is a lot of work, and we at Goldleaf are here to help. Always feel free to call or email with any questions. To start production on your custom reactor skid, please fill out this Custom Request Form to explain what you need. A phone consultation and quote will follow shortly after.
Goldleafs mission is to provide the perfect lab solution to any scientific application, so please feel free to reach out for any help designing your new system. Send us you plans and requirements for your system, and we will build it for you!
Use of Glass Reactors Across Different Industries
The versatility of these machines is expansive when discussing their wide range of uses across multiple industries. Pharmaceutical, biochemical, and food production industries can all benefit from the use of glass reactors. Here is a list of different uses.
Chemical Industry
Pharmaceutical Industry
Petrochemical Industry
Food Industry
Biotechnology Industry
Safety Considerations
As with any lab application, glass reactors require a degree of safety. For starters, always ensure chemical compatibility with glassware, stirring rod, and hoses to prevent unwanted degradation. When working with potentially hazardous vapors, a fume hood or other form of explosion proof ventilation should be used to evacuate said vapors and pull in fresh air.
When installing a reactor system always consult with a professional about electrical requirements, ventilation needs, and other potential safety hazards to mitigate any risks later down the road. Goldleaf will always be available to customers who need assistance in any installation or training for their team.
Goldleaf Glass Reactors
At Goldleaf we work to ensure the safety and ease of use with our systems. That is why we provide options for explosion proof equipment when there is any volatile chemical use. Lifting reactors make loading, cleaning, and setup achievable with one operator. Any purchase of our reactors comes with a 1 year warranty and lifetime support from Goldleaf for installation, repairs, and upgrades, just let us know about anything you need help with.
Conclusion
As laboratory processes and research facilities expand, Goldleaf will be there to support the industry. Our reactors cater to an extensive range of industries and the modular options make these a versatile tool that can change as a facility changes. Call us at (510)487-1390 or email us at [email protected] for more details about glass reactors and their availability, we would be happy to speak with you.
Comments
Be the first to comment...