You have no items in your shopping cart
Homogenizers For Viscous Materials
- Posted on
- Posted in Buyers Guides, Homogenizer, How To Guides
- 1
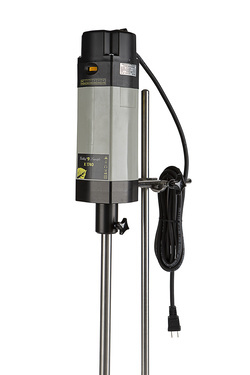
Homogenizers are key pieces of machinery used in the pharmaceutical industries. They are valuable tools for creating uniform, even mixtures of two or more substances that are combined together. Homogenizers help to mix materials that normally would not mix, such as oil and water, and they also help reduce particle sizes to provide a finer texture. Homogenization is a critical step in many processes, such as making cosmetics and drugs. These machines also play an important role in keeping the safety of consumer products by ensuring that ingredients are properly mixed and contained throughout production.
When selecting rotor stator homogenizers, it is important to note the viscosity of the solution you plan to mix. The homogenization process becomes less efficient as your samples become thicker and more viscous. A homogenizer moves liquids at high speeds at flow rate acceptable for the homogenizer shaft and users are not able to use larger volume samples as higher viscosity materials are introduced.
Best units for homogenizing viscous liquid
Goldleaf carriers a number of high end homogenizers capable of meeting needs for viscous solutions. To determine which unit is best for you, you need to know two things:
1. How viscous is your solution going to be?
2. How much solution do you want to mix at a time?
Homogenization takes about 30-60 seconds but is limited by the amount of solution that can be emulsified. Here is a guide for volumes and viscosities for our homogenizers:
Largest:
-X1740 Homogenizer: Our largest benchtop homogenizer available. Can mix 2L of viscous oils in 45 seconds. Hotplate may be needed for very thick solutions.
Volume for viscous material: 500mL - 2,000mL Maximum
Shaft needed: Shaft for X 1740, 5000-20000mL
Seal type: (G) Slide
Blade Type: (V) Viscous
Medium:
-X1000D Homogenizer: Our medium sized benchtop homogenizer, good for smaller size facilities doing occasional testing but not day to day production.
Volume for viscous material: 500ml - 1,000mL
Shaft needed: Shaft for X 1000D, 20mm
Seal type: (G) Slide
Blade type: (V) Viscous
Smallest:
-X 120 Portable Homogenizer: The smallest homogenizer we carry, meant to be a hand held unit. Great for on site testing, bring with you when visiting producers. Not meant for large scale production.
Volume for viscous material: 100mL-250mL
Shaft needed: Homogenizer Shaft for X 120
Seal type: (T) 17
Blade type: (V) Viscous
Size: 150mm
What is viscosity and why is it important?
Viscosity is measured in centipoise (cP). Water based solutions and solvents have a relatively low viscosity, around 10 - 100 cP. Mixing liquid at this low of a viscosity is very easy with a high shear homogenizer, and you will select the size of the homogenizer based on the amount of liquid you want to mix at once.
A small handheld homogenizer can do about 500mls of thin liquids, and a larger benchtop model can handle up to 20L. The maximum cP most rotor stator homogenizers can work with is 10,000cP.
When looking at a homogenizer, the specifications will likely display a total amount the unit is capable of mixing. It is very important to not this measurement is made based off thin liquids.
The homogenization process changes based on the viscosity of the liquid or material you are mixing. If the fluid is very dense and thick, the homogenizer can only do a lower volume. The same homogenizer than can process 20,000ml of thin liquids will only be able to produce 2,000ml of a thicker fluid that does not flow easily. Production can be sped up by processing at higher temperatures, which will be discussed in detail later in the article.
How viscous can your solution be?
Different types of viscous materials can be homogenized at different amounts, the total sample size will decide the efficiency of the homogenizer. As previously mentioned, the maximum cP of your solution can be 10,000cP. This is a viscosity similar to that of honey, anything thicker will not be homogenized properly. The high velocity mixing head will be significantly slowed down in a solution this thick.
For example, mixing food and beverages can be done fairly simply with a standard setup. A liquid can easily pass through the homogenizer shaft, but a thicker oil will obviously have a harder time. Going too thick can break fragile internals of a homogenizer shaft, so understanding the viscosity of your sample is key to an efficient mixing process.
How does viscosity affect the homogenization process?
As viscosity is increased, the homogenizer has a harder time mixing liquids or a fluid that does not flow easily. Different types of homogenizers are better equipped and have components for higher viscosity materials.
Viscosity is a key factor in the homogenization process and affects the rate at which a material can be mixed. A high viscosity material, such as honey or cream, must be broken down or sheared in order for it to blend properly with other components.
The higher the viscosity of your material, the more power and time it will require to achieve a desirable result. Higher viscosities also increase the risk of damaging your blades due to overheating, so careful monitoring of temperature and speed is essential.
Additionally, multiple passes may be necessary if quality particle size reduction or dispersion of components cannot be achieved in one cycle.
A smaller homogenizer will not be able to handle mixing fluids that do not have a proper flow rate. Depending on your particular application, the process of homogenizing may require an extra step.
Contact us at Goldleaf to find customized solutions, we have developed a number of homogenizer solutions for bulk amounts. We can produce a high quality homogenization vessel that has a chamber and heated jacket to better control the mixing and homogenizing process.
How to mix viscous material with a homogenizer
Processing a thicker mixture or material can be achieved at either a lower volume or higher temperature. You can place your solution on a hot plate and stir it at higher temperatures in order to lower the viscosity and increase the flow rate of your fluid or material.
Understand your solution before adding heat to ensure the product quality is not affected. Rotor stator homogenizers can handle higher temperatures as long as the processing operation is under control and the rpms from the rotor stator do not increase temperature to the point of damaging the material or homogenizer.
A liquid or fluid that has a high viscosity must be put on heat for a short time in order to increase the efficiency of production. If the liquid is not at a proper viscosity, the high speeds of the blades will cause the homogenizer to break under such high pressure. This is because when the materials are pulled into the shaft, it hardens and clogs the internals of the homogenizer.
The shaft chamber has small and fragile parts like springs and gaskets that will tear if they come in contact with foreign materials that are too viscous when homogenizing.
We have developed a homogenizer setup for processing at a certain temperature range and viscosity. To ensure the homogenizer is mixing properly, get the shaft as close to the bottom of your chamber as possible without contact and slowly ramp up the Rpm's to control mixing speed.
Mixing viscous materials with a homogenizer can be a tricky task. The key is to understand the characteristics of your material and the application you are using the homogenizer for. Here are some tips for successful mixing:
1. Make sure that you select the best possible homogenizer for your material and application. The type of homogenizer, blade geometry, and number of passes should all be selected carefully to ensure the best results.
2. Once the right homogenizer has been chosen, begin by slowly adding your viscous material into the vessel containing the homogenizing blades at a steady rate. Keep an eye on the temperature to avoid overheating which can damage your blades or reduce their efficiency.
3. Control speed when mixing viscous materials to optimize shear and turbulence needed for successful blending between blade cycles. Monitor flow, pressure and other mechanical parameters in order to reach optimal performance from either rotor stator or propeller based systems.
4. Use multiple passes through the same set up if necessary in order to achieve adequate particle size reduction or dispersion of components within a mixture or solution.
5. Clean your homogenizer after each use – viscous materials can leave behind residue which will reduce performance of future batches if not removed properly.
What is needed to mix viscous materials
Continuous operation can be more efficient by connecting a vessel to a flow through homogenizer and using gravity to force the solution through a line and pump the mixed solution into a collection tank.
Recirculation can be used to continuously process a solution ensuring the entire product has been efficiently mixed. This is achieved by circulating a flow through homogenizer to a vessel and pumping the mixture back into the container, so it continuously is pumped through the homogenizer.
Viscous materials require specialized rotor stator homogenizers that can break down the material and disperse it evenly throughout the mixture. Viscosity is a measure of resistance to flow, so higher viscosity means that more force is required to move the fluid.
Specialized cutting blades and high speeds are used to create turbulence and break apart particles. Additionally, heating elements may need to be used in order to reduce viscosity further. The result is a thinner, more uniform mixture with smaller particle sizes.
Deciding the volume for your homogenizer
Rotor stator homogenizers have both a minimum and maximum capacity for mixing, enough liquid is needed to cover the blade, but too much material will overflow the shaft. When looking at the capacity rating for homogenizers, it is usually stated in Milliliters in regards to how much water like fluid it can mix at a time.
When using a homogenizer for more viscous materials, the range of liquid that can be used is greatly reduced. This is due to the increase in energy needed for homogenizing the fluid. Although these units are fairly efficient, their efficiency in processing is based on the viscous materials being used.
If using viscous material in production, the fluid capacity for homogenizing is cut down based on the viscosity of the liquids the homogenizer comes into contact with. Be sure to control the rpms in a suitable range and keep temperatures acceptable to not damage the viscous materials and ensure product quality of your solution.
Materials that range from, 5,000 to 10,000 cP are still viscous enough to be used but must be heated first. They will also lower the homogenizing capabilities to a much lower volume of about 75%.
Contact us at Goldleaf for customized solutions based on the viscosity of your materials and we will ensure your homogenizer is equipped properly.
Conclusion of viscous homogenizing
Homogenizing viscous liquids for production is feasible when done correctly. Using the correct homogenizer and shaft will ensure product quality and production times. Whether homogenizing food, liquids, oils, or solids, Goldleafs homogenizers are top of the line quality even for viscous solutions. Call us or drop a line for help finding your next homogenizer, we guarantee our product quality and customer service.
Take a look at our cleaning guide below and see other articles about homogenizers and mixers in our blog.
https://www.goldleaflabs.com/service/disassembly-and-cleaning-of-g20g30-homogenizer-sha/
Fantastic! This article is good and informative content that gives valuable information..https://www.gaiascience.com.sg/productcategories/homogenizer-laboratory-essentials